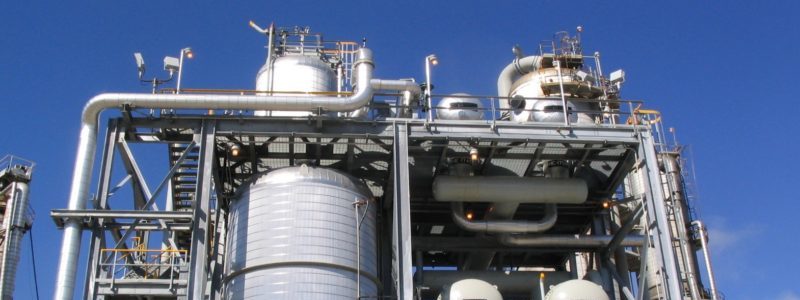
Process Chemicals Facility
Project Desciption
Adding new process equipment to a facility originally installed in the 1960s presented many challenges to the design and construction teams. Working closely with the owner and contractors, Perigon executed detail design documents for structural, electrical, instrumentation, and piping. The new process structure with caisson foundations had to be designed to fit within a very limited area with a variety of existing underground obstacles. The new structure consists of two elevated floor levels supporting several large heat exchangers and vessels.
The project required many piping tie-ins ranging from 1” to 24” in nominal pipe size. Perigon’s highly experienced piping designers successfully routed pipe thru a myriad of existing conditions to/from the new process structure. Flexibility analysis was performed utilizing Caesar II software. Piping isometrics complete with bills of materials were produced to facilitate material acquisition and shop fabrication of piping spools.
Instrument specifications and purchasing inquiries were produced for new instruments. Large valves with strict technical attributes required working closely with the owner and vendors to ensure all aspects of the design and budget were met. Wiring for controls and power was provided via new and existing panels.
Perigon also produced equipment modifications drawings for new nozzles and internals changes for three large process towers. A new cooling tower basin and p pump were also designed and installed on this project.